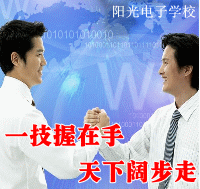
1 CAE并行设计
1. 1基本思想
以往在模具设计过程中,由于受到CAE工程师技术水平和CAE软件的限制,CAE技术主要用于分析、验证模具的结构设计,即结构设计工程师先将模具浇注系统和冷却系统设计完成,然后由CAE工程师进行CAE分析,通过流动、保压、变形分析验证浇注系统及冷却系统的可行性。这样一来,一般周期较长,当设计任务较为繁重时,无法及时完成分析任务,限制了CAE作用的发挥。通过不断地实践和经验积累,CAE工程师提高了自身的技术水平,加之CAE软件的升级更新,CAE分析的效率和质量大为提高。为进一步提高CAE技术的应用效率,我们在模具设计过程中引入CAE并行分析,不仅对制品设计进行验证,而且对模具浇注系统及冷却系统进行指导性设计,优化制品及结构设计方案,提高整个设计过程的效率。
1. 2 CAE设计过程对比
传统模具设计过程是制品、结构、数模顺序的设计。CAE分析处于模具结构设计之后,主要是对模具结构设计结果的验证,同时验证制品设计。当分析结果发现缺陷时,则需反馈给结构或产品部门进行改进,提出改进措施。但由于时间的滞后,往往会造成设计工作的重复及工作量的增加,影响了模具设计进度。
2 CAE并行设计实例
现以使用MPI(Moldflow Plastics Insight) 4.0软件设计空气取水机门盖模具为例,简要介绍CAE并行设计在门盖模具设计过程中的应用。
2. 1制品优化设计
制品 大外形尺寸为605 mm(长)×360 mm(宽) ,主要壁厚为3 mm ,筋位 薄处为0. 8mm ,浇口形式为一侧进胶。用户要求制品为外观透明制件,预选材料为透明聚碳酸酯( PC),制品收缩率为0.5 %。由于采用了模具设计并行工程,在完成制品优化设计的同时,模架设计也基本完成,在确定模具的型腔数、制品定位、模架大小后,可以根据以上输入条件设计出准确的CAE模型。此套模具采用两板模直浇口,浇口位于制品中心凹槽处。主流道尺寸为入口直径,达4 mm ,双边斜度为2°,高度为110 mm。
3结语
实践证明,通过CAE技术在模具设计过程中的并行应用,可以提供制品优化设计方案,指导模具结构设计,提高设计质量,缩短设计周期, 大限度地发挥CAE的技术优势。
